Hey! This site is reader-supported and we earn commissions if you purchase products from retailers after clicking on a link from our site.
It seems many folks buy an air compressor without considering compressor sizing and what size air compressor you need for a particular use case.
Things to be considered include what they intend to use the air compressor for, whether it should be oilless or oil-lubed, or how big an air compressor they are going to need to provide adequate compressed air to run their air tools and compressed air equipment?
For compressor sizing, it is necessary to figure out how much air you will need. That is… the air requirement for all the air tools, all the blowguns, all the air cylinders, all the air-operated diaphragm pumps, and everything that is in your plant, workshop, or garage that uses (or has the potential to use) compressed air.
Consider how much of that equipment will be operated at the same time and whether or not that compressed air demand is going to be continuous or intermittent or change as your tool use changes, production using air equipment increases, and so on.
Table of Contents
- How Can Air Compressors be Sized?
- The Key Parameters when Specifying Air Compressor Size to Suit a Particular Air Tool
- How to Size an Air Compressor For Air Tools
- Why Duty Cycle Matters When Sizing an Air Compressor
- A Worked Example of Sizing an Air Compressor
- A Worked Example – Increasing Air Compressor Tank Size to Stay within Duty Cycle
- What Size Air Compressor Do I Need?
- What Size Compressor for an Impact Wrench
- What Size Compressor for a Sandblaster
- What Size Compressor for Stucco Spraying
- What Size Compressor for Die Grinder
- What Size Compressor for Painting
- What Size Compressor for a Nail Gun
- About Published Compressor Flow Specifications
- FAQs (Frequently Asked Questions)
- Existing Questions About Compressor Sizing
How Can Air Compressors be Sized?
Firstly, let’s think about how you can size your air compressor. 6 parameters instantly come to mind, and these are:
- CFM (cubic feet per minute)
- Pressure (psi/bar)
- Tank Volume (liters/gallons)
- Power (hp / kW)
- Physical dimensions (feet/meters/footprint/volume)
- Duty Cycle (specified as a percentage)
CFM
CFM (cubic feet per minute) is the normal unit of measure for the volume of discharge air or flow rate from a compressor over time. As you may have guessed, its units are based on volume/time. Please visit our page explaining CFM for more information.
Pressure
Pressure (measured in PSI – pounds per square inch) is probably one of the units that come to mind when thinking about what size compressor you need. There are however a few different pressures to consider in the specification of an air compressor.
Working / Operating Pressure / Pressure Range
Working pressure or operating pressure is given as a guideline as to what the air compressor’s optimum performance will be at. This is typically specified as the cut-in and cut-off pressures.
The factory set cut-in and cut-off pressures (and the pressure differential between them) is often also referred to as the “pressure range” of the air compressor.
This pressure range, therefore, represents the lowest pressure the system will drop to before the air compressor pump kicks in, and the highest pressure the system will pump to before cutting out.
It is in many cases possible to adjust cut-in and cut-off pressures on the air compressor pressure switch. Importantly, and maybe obviously, the cut-off pressure (pressure at which the compressor pump stops) can only be set to be equal to the maximum pressure of the compressor and no more.
Maximum Pressure / Maximum Allowable Working Pressure
And then we have the maximum allowable working pressure (MAWP) — an important factor to consider when sizing an air compressor in relation to pressure. In relation to SIZING an air compressor, this actually is directly proportional to the number of cubic feet of air that can be stored inside the compressor tank – that is the important factor to consider here. The maximum pressure itself as a standalone unit tells you nothing. The maximum pressure in combination with the size of the tank ultimately defines the cubic feet of air storage.
Air Tank Volume
The volume of the air tank itself is of course a very common way of sizing air compressors, I will touch on this further in the worked example to follow. We have a separate page specifically on sizing compressor air tanks as it’s a key aspect of sizing the volume of air available to both small and large-scale operations.
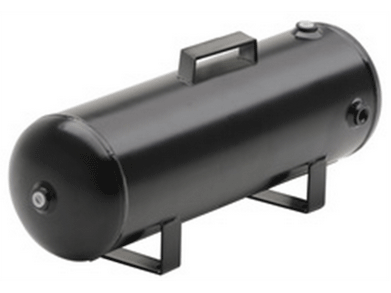
Power
The power or horsepower (hp) is a measurement of the mechanical energy an air compressor uses to complete its task of compressing air. Typically air compressors have HP ratings anywhere between 1.5 and 6.5, but some larger stationary air compressors may have up to 15 HP.
Physical Dimensions
The actual size of the whole air compressor system is probably the first thing that springs to mind when you think of the literal term “size” and applies it to an air compressor. These physical dimensions can be measured in a number of ways:
- feet
- metres
- footprint
- volume
Duty Cycle
The compressor Duty Cycle is quite an important piece of information to have when you are sizing an air compressor for your home or business workshop.
A duty cycle of 50% for a particular brand and model of the compressor would mean that this particular unit could run steadily for 10 minutes, and then it must have a 10-minute rest period before it kicks in to compress more air. More information on the duty cycle can be found on our detailed page.
The Key Parameters when Specifying Air Compressor Size to Suit a Particular Air Tool
Within those 6 parameters just presented, CFM, pressure, tank size, and duty cycle are the key parameters you should focus on when sizing your compressor.
Why? You may ask… Well, the answer is simple:
Power is just a function of CFM and Pressure, so concentrate on specifying the CFM and Pressure you need – the power rating required is just a result of specifying CFM and Pressure.
Duty cycle, as already mentioned is an important consideration, along with tank size (volume of air storage), whilst physical size (actual size of the whole system) isn’t typically a major consideration unless talking about an air compressor that must fit in your car for emergencies – or you’re fitting out a compressor room in an industrial application.
I will provide you with a worked example in this article that will help you better understand why these 4 parameters are the most important – and importantly how they interact with each other.
How to Size an Air Compressor For Air Tools
Air tools have a CFM rating typically specified at 90 PSI – however that doesn’t mean the WORKING pressure of the tool is 90 PSI – you might actually find that the WORKING pressure of the tool is significantly less (less than half) than 90 PSI. This is an important consideration to look at when buying or sizing an air compressor for your desired application.
Why Duty Cycle Matters When Sizing an Air Compressor
Duty cycle is specified typically as a percentage – see our article all about duty cycle.
Assuming the duty cycle is specified at 50% that would mean that the compressor should run for a maximum of 10 minutes, then have 10 minutes of downtime (see your own user manual for your duty cycle and time increment).
When figuring out what size compressor you need, a key consideration is making sure that the compressor stays within its duty cycle limits. It’s ENTIRELY possible that you could purchase a compressor of sufficient CFM for the tools you’re powering, but exceed the duty cycle of the compressor.
Thus you THINK you’ve sized the compressor correctly – but actually, you’ve chosen an underrated compressor for your application.
A Worked Example of Sizing an Air Compressor
This initially worked example I am providing you with is a highly simplified way of calculating whether you’re exceeding your air compressor’s duty cycle. Let’s say your:
- Air compressor has a 50% duty cycle
- Air tool has a demand of 5 CFM
- Air compressor delivery capability is 8 CFM
Under CONTINUOUS DRAW of 5 CFM, your compressor would have to work 5/8 of the time or expressed as a percentage 62.5% of the time…
So straight away, you’re exceeding the stated duty cycle of 50% for your air compressor.
This is massively simplified as I said because it takes no consideration of the air compressor tank size or storage pressure! But it gives you a good underestimate.
A Worked Example – Increasing Air Compressor Tank Size to Stay within Duty Cycle
So now let’s take that same worked example but apply some thought about tank storage pressure:
- Air compressor has 50% duty cycle
- Air tool demand is 5 CFM
- Compressor delivery capability is 8 CFM
- Air tank storage pressure is 180 PSI and outlet pressure is 90 PSI
First, let’s assume the air tank is 15 liters / 0.5 Cubic Feet @ 90 PSI
The “atmospheric” air in the tank is 90/15 * 0.5 = 3 Cubic Feet
(this is because atmospheric pressure is 15 PSI give or take (it’s 14.696 PSI) – and “90 PSI” above atmospheric, is 6 x 15)
But we’re storing at 180 PSI… So we need to double this number from 3 cubic feet to 6 cubic feet…
With the compressor at full pressure (180 PSI) there is “theoretically” 6 Cubic Feet of air at 90 PSI stored in the tank (this is an oversimplification! But, twice the pressure means there are twice as many air molecules in the tank than there would be at 90 PSI, thus, twice as many cubic feet!)
Of course, as the tank pressure needs to be above 90 PSI to deliver 90 PSI at the outlet, the “volume of air available” is once again halved – so instead of 6 Cubic Feet of air, it’s 3 Cubic feet of air…
So, now assuming the air tank is full at 180 PSI and your tool is CONTINUOUSLY drawing down 5 CFM at 90 PSI.
The tank will deplete to 90 PSI in 3/5 minutes = 0.6 minutes… Yes, that’s 36 seconds.
NOTE: The compressor would of course cut in before we reached 90 PSI to once again fill the tank and keep it above the 90 PSI working pressure at the outlet.
At 8 CFM at 90 PSI capability, the air compressor would have to work for a certain length of time to refill the tank.
Let’s assume you’re not drawing air from the compressor tank whilst it’s refilling for a second…
You’re trying to replenish 3 CFM into the tank… BUT you’re also replenishing ABOVE 90 PSI and for every PSI above 90 PSI in the tank, the compressor is going to be less efficient at compressing air. For ease (and oversimplification!) let’s call it 75% efficiency – so your 8 CFM compressor is now actually a 6 CFM compressor.
So your now 6 CFM compressor would pump 3 CFM of air in 3/6 of a minute or 30 seconds…
However, you’re also drawing air away from the system at 5 CFM at 90 PSI… So, your tank is being emptied and filled at the same time.
With your lower efficiency at above 90 PSI, your compressor is now only 1 CFM greater in capacity than your drawdown.
So to ACTUALLY refill the tank with 3 CFM – and the compressor replenishing at 1 CFM – the 3 CFM replenishment volume would take 3 minutes to refill before cutting off…
Then remember our earlier calculation on how long it would take to empty the tank back down to 90 PSI?
That’s how long the compressor would switch off for – that’s just 36 Seconds…
So with this drastic oversimplification – the compressor would run for 3 minutes, shut down for 36 seconds, and then return to running for 3 minutes – assuming the cut in pressure was at or around 90 PSI…
This is VERY imperfect maths – but it serves a purpose to think about duty cycles under CONTINUOUS USE!
The compressor pump in this example would be running for 180secs/36secs+180secs = 83% of the time!
But the duty cycle is only 50% so this setup is VERY underrated…
So how do we fix this? Surely an 8 CFM compressor is big enough?!
As you’ll see from the above calculations – the CFM of the compressor is JUST one part of the equation…
Changing the Storage Tank Size
Let’s now assume that your storage tank is actually 60 Liters (2 Cubic Feet)
NOW The “atmospheric” air in the tank is 90/15 * 0.5 2 = 3 12 Cubic Feet
(again this is because atmospheric pressure is 15 PSI give or take (it’s 14.696 PSI) – and “90 PSI” above atmospheric, is 6 x 15)
But we’re storing at 180 PSI remember – so we’ve actually got 24 cubic feet of air
Once again though, we need to deliver at above 90 PSI so we have 12 Cubic feet of air available before the air in the tank drops below 90 PSI.
NOW with 12 Cubic Feet of air available and a continuous drawdown of 5 Cubic Feet per minute
It would take 12/5 minutes (2 minutes 24 seconds) to deplete the air in the tank to 90 PSI!
So now the time that the compressor WOULDN’T be running would be 2 minutes 24 seconds – then it would run for 3 minutes (as per our previous calculation).
So the percentage “on time” would be 180/180+144 = 55%.
So we’re A LOT closer to the duty cycle limitations stated (50%) and we haven’t changed ANYTHING but the size of the air tank on the compressor from 15 liters (0.5 cubic feet) to 60 liters (2 cubic feet).
Worked Example Summary
The thing about these calculations is that they’re based on the CONTINUOUS USE of the air tool – it doesn’t sit down and rest at ANY point in the cycle.
The reality is that unless you’re using a type of tool which sees continuous use – maybe something like a wet spray paint gun – basing the CFM, pressure rating, and tank size (all worked around the duty cycle!) isn’t appropriate – it’s a very worst-case scenario.
If the ratings of the compressor were JUST about ok for continuous use and if you believed that you were only likely to be using the tool for 50% of the time you could:
- Half the CFM of the compressor and still just cover the application, or;
- Half the tank size of the compressor – however this would likely increase the cycling on and off of the compressor which might not be ideal from a duty cycle perspective either – and the longevity of the compressor pump. If the compressor is going to be on and off every 30 seconds, that’s probably a little extreme.
- Half the max storage pressure above the working pressure (i.e. in the above example, working pressure was 90 PSI, storage pressure was 180 PSI, you could take 180-90 = 90 PSI , then half that 90 PSI to get 45 PSI. Leaving you with a storage pressure requirement of 90 + 45 PSI = 135 PSI storage pressure.
You could also size your compressor and tank (keeping within the duty cycle limitations) based on the continuous use case KNOWING that you’ve got plenty of headroom to use it on a less than continuous use case.
These numbers are drastic oversimplifications and won’t be deemed accurate in the real world – but they are near enough real-world approximations to help logically size an air compressor in terms of CFM, storage pressure, and tank size – as ALL 3 need to be considered in relation to the DUTY CYCLE limitations specified by the manufacturer.
What Size Air Compressor Do I Need?
How big of an air compressor do I need?
To help Air Compressor sizing here are simpler blocks of information and further considerations.
When first venturing into the air compressor-sizing arena, folks tend to be more than a bit intimidated. There’s such a vast array of compressors, of types, of capacities, with a veritable feast of accessories; it’s easy to become confused!
And, though there are many manufacturers of compressors worldwide, all are focused on selling their own products, which may impart a certain bias to the information that’s available from them about their compressor-sizing, you think?
So aside from the worked example, I’ve provided you with, here are some simpler blocks of information and answers to questions that may help you.
What Tool or Device is The Compressed Air For?
Have you determined what you’ll be using compressed air for? In order to correctly size your compressor, you really must do some homework towards figuring out the volume of compressed air you will require for your specific tools or amount of tools.
Is the CFM Requirement a Continuous or Intermittent Demand?
If it is necessary for your plans to run all of those compressed air using appliances at the same time, and for long periods of time, “continuously” so to speak, then you are going to require a much bigger compressor than if they are used intermittently and sporadically.
If your compressor is for continuous air use then start making a list of everything in your plant, workshop, or home that uses air, and leave a space beside each to note the expected CFM demand for each. Better yet, use a spreadsheet so that the air consumption numbers can be set up to give you a running total of the air you’ll need.
What’s the smallest air compressor for air tools?
Air tools have a high variation in CFM or SCFM requirements and also working pressure. To establish the smallest air compressor you can use with your air tools, you’ll need to review the CFM and working pressure requirements of each air tool – then specify your compressor size to suit the CFM and working pressure of the air tool with the highest CFM demand whilst keeping within your compressor duty cycle.
Remember – the CFM requirement will not only depend on the CFM rating on the tool but also whether the air tool use is intermittent or continuous.
Rule of thumb for smallest air compressor for air tools under continuous use
If the CFM requirement of the air tool is continuous it’s likely you’ll need an air compressor pump with a CFM rating of 2 x the tool’s CFM rating – this should (with an appropriately sized air tank) keep you just within a 50% Duty Cycle rating for the air compressor. (be sure to check the duty cycle of your air compressor)
Rule of thumb for smallest air compressor for air tools with intermittent use
If you assume that intermittent use means that the CFM demand of the air tool is required 50% of the time, buying an air compressor with a CFM rating equal to the CFM requirement of the air tool (with an appropriately sized air tank) should keep you also just within a 50% Duty Cycle rating for the air compressor.
Air Tool CFM Requirements & Compressed Air Consumption
Know that compressed air consumption of tools (Air Tool CFM Requirements) varies depending on the size of the air tool, its speed and the efficiency of that air tool. You need to get the specific compressed air demand for that air tool from the manual or the manufacturer of the tool for an accurate assessment of the overall compressed air demands of your shop.
Grinders will have changes in consumption due to grinding wheel size, and rotary sanders will have their consumption change due to the pad size. Even the same tool from two manufacturers will have different air consumption rates.
You may find the chart below handy in approximating the CFM requirements of an assortment of standard air tools. This is a general guide only for that standard 90 PSI pressure. Your actual consumption of compressed air will vary, depending on your tool size and design.
Air Tool CFM Chart
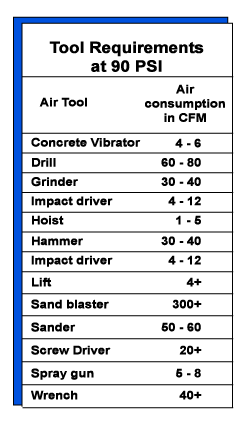
The chart above is just a rough guide, and may not accurately reflect the air consumption of the air tool planned to be used.
The best source is to get the air consumption figures for a specific air tool from that tool’s manual. Failing to find that, contact the manufacturer! They should be able to give you the exact consumption. If contacting the manufacturer, have the model number and the serial number of the air tool at hand because they will most likely ask for that.
Consider “factoring in” the highest air consumption figures you find for the tools you expect to use. You may oversize your air compressor capacity by doing so, but under-sizing the compressor you purchase may bring greater long-term costs to your plant or workshop as you grapple with air tools or air cylinders that do not run as expected due to a lack of compressed air supply.
Long Air Lines Mean Pressure Drop
The sizing calculations we have presented above are under the assumption that you are using a reasonably lengthy air compressor hose, but if you’re using a particularly long hose or hoses linked together with multiple connections you will have to consider pressure drop along the length of your hose and the connections.
Industrial plants have air compressors generating excess pressure and flow for the inevitable over-line air pressure drop. This helps to ensure that they have sufficient compressed air pressure and volume at their end application to keep their equipment running satisfactorily. The compressor you pick has to have this capability if it is an issue in your plant.
Again, some manufacturing plants will maintain a 20-30 PSI “safety margin” in extra compressed air pressure from the receiver, to help ensure that none of the plant equipment gets starved for air whether through pressure drop, leaks in the line, too much equipment being run at the same time, miscellaneous use of compressed air and so on.
This may not apply to most home users as most home users will be using their air compressor that is running in their garage and will be stood around 3 ft from it. If not, please consider it as advised.
How Much Room Can The Compressor Take Up?
As mentioned, air compressors with large storage tanks can take up a lot of space. It is important to choose an air compressor that fits in your desired space, if space is small find a smaller compressor etc. A 5-gallon portable compressor will fit in almost any location whilst a 50-gallon stationary compressor will not and will only be suitable in big enough spaces. However, this is not necessarily down to the gallon size, but more about the fact the bigger compressor will have a more powerful motor.
What’s The Available Power Source?
When selecting the compressor it is also very important to know what power source you will use for running it. Air compressors can either be powered by an electric motor or gas engine.
Is the air compressor you need capable of being plugged into a standard home outlet? Well, most are! However, some larger electric motor compressors may require a source of volts up to 240.
A gas engine running your compressor can provide more freedom as you can have compressed air almost anywhere. They will tend to be found in locations where electricity is not readily available like on construction sites. Gas engines have advantages in their flexibility of location however, they tend to be quite big so the ability to move them may become quite difficult.
Other Compressed Air Use
Air tools are only one of many applications in a plant that consume air. It’s necessary to give consideration to all of the ways that you will consume air in your plant and home applications.
Some folks don’t consider an air-driven blowgun as an air tool, yet these can sometimes use more compressed air than expected. So it is important to be aware of these considerations before sizing your compressor.
What Size Compressor for an Impact Wrench
Most impact wrenches have a recommended operating pressure of 90 PSI. Along with the pressure, each tool has a specific volume of air that it requires to operate (CFM rating). So, the CFM rating of your impact wrench will typically depict what size air compressor you need as almost all compressors are capable of providing 90 PSI.
For a small impact wrench which only requires between 3-5 CFM, you could purchase an air compressor that is rated 5+ CFM and potentially be able to provide these tools with continuous use if the compressor has a 100% duty cycle. If the compressor has a 50% duty cycle and therefore, only has an output of 2.5 CFM then you would only be able to power the impact wrenches intermittently which, would probably be fine if you’re using the tool at home.
Now, for a larger impact wrench which requires around 8 CFM to function efficiently and, you will need to purchase a compressor with 8 CFM or greater if it has a 100% duty cycle and is rated for continuous use. For use in a non-assembly line environment, a compressor with a far lower duty cycle will suffice as you will not need to use the tool as frequently.
For more detailed information on this, visit our What Size Air Compressor Do I Need For Impact Wrench? guide!
What Size Compressor for a Sandblaster
Sandblasters typically require between 90-100 PSI and are available in a variety of CFM ratings. It’s important to not exceed the maximum operating pressure or operate on a pressure that is too low when sandblasting as this can significantly affect the job. The small sandblasters can only require around 6 CFM, with larger ones being double that at 12 CFM.
The size of the compressor you need will typically not only depend on the CFM rating of your tool but the amount of sandblasting you need to do. If you don’t mind your progress being disturbed by having to allow your compressor to play catch up then a 50% duty cycle will suffice.
If you wish to have continuous use of your sandblaster then you will require an air compressor with the same or slightly greater CFM rating of your tool, and a continuous use 100% duty cycle rating.
Visit our What Size Air Compressor For Sandblasting? guide for more specific information!
What Size Compressor for Stucco Spraying
Stucco sprayers will typically require around 25 PSI of pressure and an air volume of between 5-7 CFM. If your compressor air tank is big enough to have enough air reserve to keep supplying the stucco gun while the compressor is working to keep up with the compressed air demand, you’ll be fine.
For more information visit our Air Compressor Size For Spraying Stucco & Plaster – CFM Requirements guide!
What Size Compressor for Die Grinder
The majority of die grinders, regardless of their CFM, will require an operating pressure of 90 PSI. Mini die grinders may only be rated for 3 CFM and so, most small air compressors will be able to comfortably provide this volume of air.
Other die grinders, the bigger ones which are rated upwards of 10 CFM, will of course need a larger air compressor, with a sufficient tank size. Depending on whether you wish to carry out continuous or intermittent use of your die grinder will help you gauge what CFM rating you require. Die grinders in a non-assembly line environment are likely to be used less than 50% of the time drawing its full CFM rating and so, with this, you can purchase a smaller compressor that you know will be capable of providing the intermittent power.
Visit our What Size Air Compressor Do I Need For A Die Grinder? for a more detailed description of what size compressors are suited to small, medium, and large die grinders.
What Size Compressor for Painting
Spray painters often require low operating pressures of between 20 PSI and 50 PSI to work effectively. This is no problem for you, as your compressor can be run at its normal 90-100 PSI and dialed down with a regulator just before the spray painter for use.
Spray painters are available in HVLP (high volume low pressure) and LVLP (low volume low pressure) models, which vary from as low as 4 CFM and up to around 20 CFM. Depending on the painting job you have at hand, this will depict the size of the spray painter and compressor required. If you’re simply painting a few models intermittently, then you won’t require a lot of CFM. But if you wish to spray paint a car, maybe a complete new paint job, then you will need a greater volume of air. For more information on this visit our Choosing An Air Compressor For Painting Cars – What Size, Which Is Best? guide!
For a small spray gun with low average air consumption of around 4 CFM being used to paint models, you should be able to use any small air compressor with between 3-5 CFM and a 50% duty cycle. For a larger spray painter with a rating of around 12-15 CFM for painting a car, you would want to purchase a larger compressor with a decent size storage tank.
Visit our What Size Air Compressor Do I Need For Spray Painting? guide for more detailed information!
What Size Compressor for a Nail Gun
For most nailers, air compressors are capable of putting out pressures around 120 PSI so that your nail gun works effectively. On top of the air pressure, you must have enough airflow to keep up with the nail gun’s requirements. A small compact air compressor with a 1 HP motor can provide around 2 CFM, which may be enough to allow you to drive nails with a framing gun at a 15 per minute rate.
The same compressor will reliably drive a smaller brad gun at around 60-70 nails per minute or even greater. If you intend to drive larger nails, then you will need a compressor with greater CFM. As well, if you plan to run multiple guns off one compressor, be sure to plan for double the air capacity. For further information, visit our Compressor for Nail Gun guide.
If you wish to learn more about the various nail gun types, we have a Types of Nail Guns Guide – Brad Nailers And More which is very informational!
About Published Compressor Flow Specifications
Be careful when you are getting the airflow specifications on compressors, as some manufacturers size their compressor discharge rates as if the unit was pumping free air. As air pressure in the tank or mains air is compressed, the compressor pump has to work harder. A compressor might show a CFM rating of 8 for example, but reading the fine print will tell you that it generates 8 CFM at a much lower pressure rating than the pressure you may require.
Industrial systems (actuators/air tools) often require about 90 PSI to work to their capacity. Some will require higher pressure, and some lower, of course, depending on the work each has to perform. This is because air compressors are typically rated at 90PSI as you can see on this Amazon listing below of a BILT HARD Air Compressor that is rated 4CFM at 90 PSI.
You will be using an air regulator at the point of compressed air use, to dial down the pressure and run the air equipment at the lowest possible effective pressure level. You may save substantial energy costs in doing so. For more on regulators needed for this size of air compressor please visit our regulator guide.
FAQs (Frequently Asked Questions)
Coming soon…
Additional CFM reading:
- SCFM Vs ACFM Vs ICFM – What’s The Difference? Converting & Calculating
- Best Ways to Increase CFM On Air Compressors
- Connecting Two Air Compressors Together
- How to Calculate CFM of Air Compressors
- CFM Pipe Size Chart
- SCFM vs CFM for Air Tools & Air Compressors Guide to Compressor Ratings
- What Is CFM and What Does CFM Mean on An Air Compressor?
- Air Compressor Size For Spraying Stucco & Plaster
- Does a die grinder require low or high CFM?
- Speedaire 4B247 swapped with 2Z499 and its effect on CFM?
- 20 CFM Air Compressor – Buying, Hiring, What Can They Run?
- Air Compressors That Produce 500 CFM And Above
- CFM SCFM PSI Compressor Flow Issues
- Ingersoll Rand Type 30 model 242 HP and CFM?
- CFM rating of Black Max compressor
What size air compressor:
- What Size Air Compressor Do I Need For Impact Wrench?
- What Size Air Compressor For Sander?
- What Size Air Compressor For Sandblasting?
- What Size Air Compressor For Framing Nailer?
- What Size Air Compressor For Air Hammer?
- What Size Air Compressor For Air Ratchet?
- What Size Air Compressor for Car Detailing?
- What Size Air Compressor for Truck Tires?
- What Size Air Compressor For Nail Gun
- What Size Air Compressor for Painting Cars?
- What Size Air Compressor Do I Need for Spray Painting?
- What Size Air Compressor For Staple Gun Or Upholstery Air Stapler?
- What Size Air Compressor Do I Need For A Die Grinder?
If you’re wondering how to plumb an air compressor setup, visit our guide!
Existing Questions About Compressor Sizing
How is the Average SCFM for an air tool calculated? Is there a formula?
by James Toland
(Cincinnati, OH)
How is the Average SCFM for an air tool calculated? Is there a formula?
Answer
My Response: James, not to my knowledge.
It’s like asking if there is an average motor size in all the cars in the world.
Each manufacturer of air tools builds their tools to provide a certain amount of force to do the job that tool is supposed to do.
Another manufacturer of that same type of tool will make a DIY model with less force and lower-cost components.
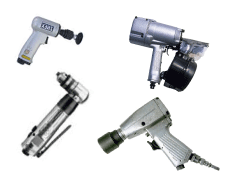
Another manufacturer will make the same type of tool but in industrial-strength size.
Each will use different levels of flow.
On the pages on this site is more information about airflow, CFM and of course, this page about compressor sizing
The pages provide a guide of some air tool usage as well.
Yet, the only thing you can do for sure is to pick the tool, read the manual and or specification plate, and see what that air tool requires in flow and pressure.
Then, if you give it that, the tool will work properly. If you don’t, it’s like feeding the carb (my, that does date me doesn’t it) with too little fuel when you step on the gas in the car. The car will not run properly.
Neither will your air tool.
If you have any questions regarding what size air compressor you need, please leave a comment below, with a photo if applicable, so that someone can help you!