Hey! This site is reader-supported and we earn commissions if you purchase products from retailers after clicking on a link from our site.
What is a compressed air tank and how do you know if you need an air receiver tank? Well, this guide will give you all the ins and outs of what air receiver tanks or otherwise known, storage tanks are.
Not only that, but I’ll explain to you how these air receiver tanks with compressed air, and how they can be used to maximize the efficiency within your own compressed air system.
Table of Contents
- What is a Compressed Air Tank? Air Accumulator Tank, Air Receiver Tank?
- How Does a Compressed Air Tank Work?
- Compressed Air Tank Sizes and Ratings
- Sizing a Compressed Air Tank
- The Purpose of an Air Receiver Tank
- Efficiency Benefits of Air Receiver Tanks
- How Much Air Storage Capacity Do You Need?
- FAQs (Frequently Asked Questions)
What is a Compressed Air Tank? Air Accumulator Tank, Air Receiver Tank?
A compressed air receiver tank (also known as air tank or compressed air storage tank) is everything you think it sounds like… it is a tank that receives compressed air and stores it after it exits the air compressor. This process provides you with an extra load of compressed air that you can draw upon without having to run your air compressor.
An air receiver tank is a type of pressure vessel that holds compressed air under a certain amount of pressure for future uses. Air tanks are typically cylindrical in shape so that they reduce stresses in the “skin” of the tank, as a result, they are often equipped with feet welded to the tank. These can be welded to the dished end of the tank in the case of vertical compressed air tanks or on the curved side of the air tank in the case of horizontal tanks.
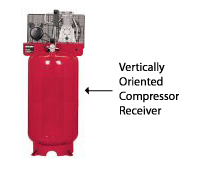
The tank itself can be portable if required, but in many cases, it is stationary and mounted to the floor using anti-vibration mounts to isolate any vibrations caused by the pump and motor during its operation. The air tanks come in a wide array of sizes, with their configurations being either vertical (above) or horizontal (below).
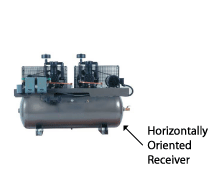
If you are wondering whether you lay your air compressor tank down, please visit our guide for more information! Sometimes, you may wish to connect two air tanks together.
How Does a Compressed Air Tank Work?
Compressed air tanks are sealed volumes that are typical of a welded construction strong enough to contain the required pressure. They’re filled by a compressor unit, typically mounted on the tank itself – and they discharge air into compressed air piping systems via an outlet.
An air compressor typically operates on a demand basis. When air is required, a pressure gauge/switch on the downstream side of the compressor tank checks the pressure in the compressor tank and, by extension, the pressure in your air system airlines.
As demand downstream makes the pressure in the airlines drop, the pressure in your compressor air tank will also drop. When the air pressure in the tank drops low enough it reaches the cut-in pressure level, and the pressure switch will send power to the motor to start compressing more air.
When the pressure in the downstream line and the air receiver tank reaches the high-pressure cut-out set point, the compressor stops.
The difference between the two pressures and the speed at which the compressed air pressure changes between the two set points dictates how often the compressed air system fires up.
Compressed Air Tank Sizes and Ratings
Compressed air receiver tanks as mentioned, are available in a variety of different sizes. These varying sizes provide varying capacities of compressed air, which tends to be measured in gallons.
The peak demand or most common sizes include 5,7,9,10 and 11-gallon air receiver tanks. The smaller the air tank (gallon number), you guessed it, the smaller the air compressor, and the easier it is to transport or have portable air. The bigger the air tank, the more suited it may be for most applications but the more difficult it will be to move.
To discuss and understand capacity, I’d like you to note that one cubic foot of volume equals a 7.5-gallon air receiver tank’s volume. Now, imagine a standard small car in your mind and its small tires. These tires have an approximate volume of one cubic foot. Therefore, a 7-gallon air receiver tank simply does not have the capacity to fill a small car tire when it is completely flat, but an 8-gallon air receiver tank does.
In regard to ratings, compressed air receiver tanks have a maximum pressure rating that is measured in psi (pounds per square inch) The most common ratings tend to range from 125psi to and beyond 150psi. The psi rating indicates the pressure at which the air receiver tank can safely handle and operate efficiently without putting itself or anyone’s safety in danger.
I must recommend to you, however, do not fill your tank up to the maximum pressure level because air pressure within your compressed air systems will rise with the heat.
Sizing a Compressed Air Tank
A general rule of thumb for air compressor receivers or compressed air accumulator tanks is that they should have approximately 1 gallon of capacity for every CFM of the air compressor output. For example, since a 25 HP compressor can theoretically generate about 100 CFM at 90 PSI, the air receiver for that compressor should be 100 gallons in size.
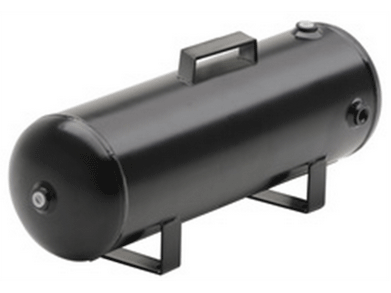
The receiver size relative to the downstream demand will allow the compressor to build up a reservoir of compressed air at the desired pressure in the receiver and have it in reserve so that the air compressor does not have to start every time air is used.
The air receiver tank’s volume will exceed all downstream demand for a period of time. Therefore, once the receiver is filled, your air-driven equipment downstream from the compressor can – perhaps – cycle on and off a number of times without the compressor having to cut in every few seconds to maintain the downstream pressure set point.
It is important to ensure the air tank receivers’ size is large enough that the compressor has rest time, not just to help prolong compressor life, but also for additional benefits to having large air tank receivers. Sometimes, you may be able to connect two air tanks together.
Air Receiver Tanks for Portable Air Compressors
I’ve provided you already with a general rule of thumb to use on any type of compressor. Now, I will be a little more specific.
When dealing with a reciprocating air compressor, it can be said that you’re to take the tool with the highest CFM requirement at your required PSI, and multiply that CFM number by 1.25 or 1.5, let’s say 1.5 to play it safe. You would then round up the resulting number to the nearest gallon size for your tank.
It may be more difficult to size an air receiver tank for say, a rotary screw air compressor, as these designs are made to supply a continuous stream of air without the need for a storage tank.
They may, however, wish to use an air receiver tank to give the air compressor a much-needed boost to higher CFM tools. For example, if your tool requires 50CFM, but you have a 40CFM air compressor, then you could choose an 11-15 gallon air receiver tank to compensate for that 10CFM difference and have a little extra to be on the safe side. This addition can help save you money in the long run.
Air Receiver Tanks for Stationary Air Compressors
Being able to properly size an air receiver tank for stationary applications is a far more complex task, and I would recommend speaking to a qualified engineer for advice. Stationary air receiver tanks should be sized in accordance with their volume and pressure variations in air consumption, from peak demand to low demand. Other considerations include:
- air compressor size
- control system strategy (modulation or on-off control system)
- pipe size and length
Calculating Air Receiver Tank Size
A rather commonly used formula to calculate an air receiver tank size is:
t = V (p1-p2)/C pa
Where:
- V = volume of the receiver tank (cubic feet)
- t = time for the receiver tank to go from upper to lower pressure limits (sec/min)
- C = free air needed (scfm)
- pa = atmospheric pressure (14.696 psia)
- p1 = maximum tank pressure (psia)
- p2 = minimum tank pressure (psia)
This formula can then be rearranged to give you an approximate ideal volume of your receiver tank:
V = t C Pa/(p1-p2)
It is recommended that this formula is only used for large air compressors, particularly of the reciprocating sort.
Identifying the maximum consumption of your air compressor is very important when sizing an air receiver tank. In an ideal situation, I’d recommend that your air receiver tank provide enough air to exceed your maximum consumption and play it safe.
To calculate your maximum consumption in the system, or otherwise known as your free air needed “C”, you need to add together each air demand of the tools that will be used simultaneously. Once you have done this, you multiply the summarized consumption with a utilization factor.
Now you may ask “but what is the utilization factor?” well let me clear that up. The utilization factor is the way in which a tool is used and how that affects the airflow through it.
This utilization factor is quite simply the difference in CFM load and time interval between applying the tool to do its job. It allows for some air receiver tanks to meet the heavy short time demands of certain equipment at larger volumes than the installed compressors supply capabilities.
Pressure Band
One more consideration when calculating the ideal air receiver tank size is the pressure band (differential). It’s important to have a slightly greater amount of pressure set to deliver from the compressor than what the consumption process requires. This is so that the excess can be stored ready for if the demand increases.
Pressure and flow controllers can be used after the air receiver tank for stabilizing downstream pressure and flattening demand peaks.
The Purpose of an Air Receiver Tank
An air receiver tank has the sole purpose of providing temporary storage for compressed air. It can also help your compressed air systems to run more efficiently. The air receiver tank has many functions and purposes in your compressed air system:
- It stores air that can be used for short-term, high air demands- for example, if you need a short-term high flow rate of around 15CFM, but your air compressor only generates 3CFM, then you require a tank to get that 15CFM instantaneous.
- It can provide consistent pressure so that tools and services operate within their bandwidth of air flow
- It provides a steady air signal to compressor controls
- When they’re used as a “wet tank” as such, they can help remove water from the system through a natural condensation surface. Acting as a secondary heat exchanger, after giving the air a chance to cool down, condensate and then the water can be removed by the dryer at the exit. This’ll increase the efficiency of the tank and air dryer
- It can reduce cycling of the compressor on and off- this can lead to significantly increased efficiency and environmental benefits
- It can provide you a reservoir of backup air that could be called upon to safely run down pneumatic tools in the event of a power loss – for example, within an industrial setting, air receiver tanks will be called upon to return pneumatic tools to their safety/neutral position so that no energy is left in their system
If you’re interested in Cleaning the Inside of Air Compressor Tank, visit our guide!
Efficiency Benefits of Air Receiver Tanks
Adding an air receiver tank to your compressed air systems can significantly improve your efficiency. They do so by:
- Increasing the efficiency of the air dryer by reducing the moisture build-up
- Lowering the pressure requirements for the air compressor and air system
- Reducing the waste of compressed air from excessive sump blowdowns
How Much Air Storage Capacity Do You Need?
You might ask how much air storage capacity I need? and the answer is certainly not that simple one… The volume of compressed air storage capacity needed by you depends on the following few factors:
- What applications do you intend to use the compressed air system for
- What diameter is your intended piping
- The consistency of the airflow in your compressed air system
- Your air compressor capacity in CFM (cubic feet per minute)
- Peak CFM requirements at the point of maximum demand
FAQs (Frequently Asked Questions)
To keep it simple, compressed air tanks are sealed volumes built to contain a required pressure of air. They’re filled by an air compressor unit, which in most cases is mounted on the tank itself. The tank stores the pressurized air and discharges it into the compressed air piping systems via its outlet when in use.
In order to calculate the size of a compressed air tank you must use the formula “t = V (p1-p2)/C pa“. Where: V = volume of the receiver tank (cubic feet), t = time for the receiver tank to go from upper to lower pressure limits (sec/min), C = free air needed (scfm), pa = atmospheric pressure (14.696 psia), p1 = maximum tank pressure (psia), p2 = minimum tank pressure (psia).
If you have any questions regarding compressed air tanks, please leave a comment below, with a photo if applicable, so that someone can help you!