Hey! This site is reader-supported and we earn commissions if you purchase products from retailers after clicking on a link from our site.
One of the most important components of an air compressor is the air pressure regulator. Air pressure regulators, otherwise known as pressure-reducing valves, are used in compressed air systems to help reduce and control the pressure in the airflow to meet your pneumatic tools requirements at the end of the line.
I will provide you with information on what Air Compressor Pressure Regulators are, how they work, and the different types of Pressure Regulators available for air compressors.
Table of Contents
- What Is an Air Compressor Regulator?
- How Does an Air Compressor Regulator Work?
- Types of Air Compressor Pressure Regulators
- Air Compressor Pressure Regulators Are Pulse Dampening
- Save Money With Air Compressor Regulators
- Air Compressor Regulators Readily Available on Amazon
- About Air Compressors Regulators Video
- FAQs (Frequently Asked Questions)
- Reader Questions and Responses
- Existing air compressor pressure regulator questions:
What Is an Air Compressor Regulator?
An air compressor pressure regulator is very important to regulate the air pressure that flows from the compressor tank into your pneumatic tools. They can adjust the air pressure needed for different pneumatic tools, as they all may require different levels.
Therefore, the air compressor pressure regulator protects the tools from being overpowered, helping to ensure the high quality of your pneumatic applications.
When operating at its optimum, air pressure regulators maintain a constant output pressure regardless of the variations in input air pressure and downstream equipment flow requirements.
Unless it is a specially built regulator being used, compressed air is normally meant to travel through an air regulator in one direction only. That direction is commonly shown somewhere on the unit with an arrow.
The regulator will usually have an air gauge that visibly indicates the air pressure setting for the airflow to the downstream side of the regulator.
Note: Air pressure regulators in compressed air systems can only lower the air pressure. Dialing the pressure up past the supply line pressure cannot increase the downstream pressure past the tank pressure level, despite how many times you turn the knob!
Air compressor regulators can be found within a combined system that has filters and lubricators as well. For more information visit our FRL Air Compressor Filter Regulator Lubricator Guide.
How Does an Air Compressor Regulator Work?
For the sake of simplicity, I have not included a gauge in the drawing below, and only showed the theoretical flow path of the regulator, to give you an idea of how they actually work.
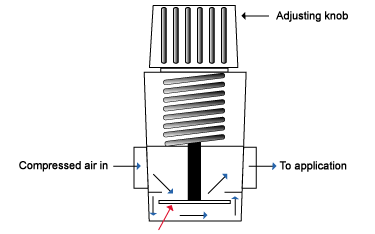
This seal moves up and down, reacting to spring pressure or air pressure as the air supply pressure varies, and the seal moving against or away from the seats, allows more or less air to flow through the regulator. Lessening flow allows pressure to drop, and increasing flow allows pressure to rise.
The regulator acts very quickly, increasing or decreasing the flow of air through itself so that the downstream pressure remains fairly constant. The accuracy of the air pressure downstream of the regulator is directly related to the quality of that air regulator. Lower-cost regulators have a wider degree of accuracy and response time than premium and precision air regulators.
Types of Air Compressor Pressure Regulators
Air pressure regulators are used for controlling pressure to a whole variety of pneumatic tools, and typically are available as either type:
- Relieving
- Non-relieving
Relieving type regulators allow for high pressure to be adjusted to low pressure even in dead-end situations. They relieve the excess downstream pressure into the atmosphere, causing a loud hissing-like sound that you’ll be able to hear.
On the contrary, non-relieving valves do not allow the excess downstream pressure to be relieved into the atmosphere. But, you need to still release this trapped air somewhere right? So, a downstream valve would need to be introduced.
General-purpose regulators can be expected to maintain an average pressure level range within a plus or minus 2-5 PSI.
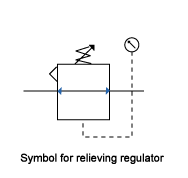
Precision regulators can usually hold a line pressure within plus or minus 0.5 – 1.5 PSI of the set point. If you need a precision pressure setting for an application, know your pressure variation tolerance, and inform the regulator supplier, to make sure you get one that works for you. And yes, precision regulators are more expensive than general-purpose regulators.
Larger pressure regulators can be air-piloted, and slaved, to smaller, remotely installed, regulators that allow pressure adjustment of a regulator in a hostile environment by one that is installed in a more benign location.
Regulators can be supplied with accessories such as locks, are supplied with or without gauges, are available in electronic formats, and in a host of configurations for specific applications.
The air compressor pressure regulator “types” do not stop here, as we also have the variation in design that I will discuss in greater detail below.
Poppet-Style Valved Regulators
The simplest and least expensive type of air regulator uses an unbalanced-poppet-style valve. This design does not have a separate diaphragm chamber is non-relieving and incorporates an adjustment spring.
When the adjustment screw or regulator knob is turned at the top of this regulator to adjust air compressor pressure, the spring is compressed, forcing the diaphragm to move and thus pushing a poppet to uncover its orifice plate.
The poppet throttles the orifice opening to restrict the flow and produce the desired amount of downstream pressure. As the pressure rises downstream, it acts on the underside of the diaphragm, balancing it against the force of the spring.
The spring under the poppet ensures that the valve closes completely when no flow exists.
Diaphragm Chamber Regulators
These types of larger and more expensive regulators incorporate a separate diaphragm chamber. The separate diaphragm allows the primary airflow to minimize its abrasive effects and can also help extend the valve’s life.
A diaphragm chamber pressure regulator consists of an aspirator tube that is exposed to the output pressure.
As flow increases through the regulator, this tube creates a slightly lower pressure in the diaphragm chamber, causing the diaphragm to deflect downwards and open the orifice without significantly reducing the output pressure.
This style of pressure regulator has minimal pressure drop across it. Larger diaphragms have increased response and sensitivity compared to smaller diaphragms.
Balanced Poppet Regulators
Another type of air compressor pressure regulator is the balanced poppet, which tends to have the same design as a separate diaphragm type but has a larger orifice to allow for greater airflow.
For them to maintain good stability, the poppet is pressure balanced. This pressure balance cancels out the fluctuations of output pressure helping to improve response and sensitivity.
Precision Regulators
A final type is the precision regulator, which often employs several isolated diaphragms that act against the flapper valves and nozzles in a balancing principle. Precision types of regulators are normally manufactured in limited flow capacities with smaller connection ports.
Considerations When Selecting the Right Air Compressor Regulator
To correctly size a regulator for your desired applications, the downstream equipment flow, and pressure requirements must be determined. Selecting the best type of regulator for your specific application will first require you to go over these styles mentioned.
Smaller regulators will commonly be of the direct-acting non-relieving type whilst most standard-sized regulators will be self-relieving, separate diaphragm chamber style. Next, the desired airflow must be considered.
Then you can select your desired adjustment screw, between a tamper-resistant locking tee or push-lock plastic knob type. The latter is the most common for general use, where operating pressure can be adjusted without tools.
Air compressor pressure regulators can also be sized based on their orifice flow rating (body size) and their connection sizes. Larger body regulators will produce better setting sensitivity and less droop than smaller body ones under the same operating conditions.
Air Compressor Pressure Regulators Are Pulse Dampening
Compressed air is a fluid. Pressure exerted at any one point in a closed system will be transmitted equally, and felt, throughout the entire system.
Therefore, each time your air compressor cycles on it starts building pressure in the system receiver and lines again, and that sudden increase in pressure will generate a pressure-pulse in the compressed air throughout all your lines in the plant. This may be negative to your application.
Having a compressor tank or air receiver on the compressor will dampen the pressure pulse somewhat, but not entirely.
For example, let us decide that the set points on a compressor are 120 PSI on the high side and 100 PSI on the low side. If you set the regulator to 90 PSI, in theory, that application should never see a pressure fluctuation, regardless of how many times the compressor kicks in or out. Since the pulsation is occurring at the 100 PSI level, which is above the regulator setting of 90 PSI.
This pressure-pulse dampening can have benefits in terms of more consistent cycling of air cylinders, and more consistent rod speed, for example.
Compressed Air Demand & Supply
The exception to this will be if the demand for compressed air outstrips the ability of the compressor to supply it.
When this occurs, the available air pressure from the tank will continue to fall, eventually moving lower and past the regulator setting. The regulator gauge reading will reflect that pressure drop, as will the compressed air in the lines to the air using applications/air tools.
When the compressed air demand stops, air pressure will start to build, and a pressure pulse can occur in the lines until the pressure is up past the original regulator set point.
Save Money With Air Compressor Regulators
Another great benefit of using an air compressor pressure regulator, and why you would want many throughout your air system, is saving money. Adjusting the pressure down to the lowest functioning level at each air-using application, you can save significant dollars in compressed air generation costs.
As an energy source, compressed air is one of the most expensive as it uses other forms of energy in its own generation. Running every cylinder and every air tool at its lowest satisfactory pressure setting will save money, for sure! And to do that, you need a regulator.
Air Compressor Regulators Readily Available on Amazon
I have picked out a few air compressor pressure regulators that are available on Amazon and may match your requirements!
The first is the apex tool replacement pressure regulator suitable for Bostitch, Husky, Hitachi and Craftsman compressors.
- Add custom text here
Prices pulled from the Amazon Product Advertising API on:
Product prices and availability are accurate as of the date/time indicated and are subject to change. Any price and availability information displayed on [relevant Amazon Site(s), as applicable] at the time of purchase will apply to the purchase of this product.
The second is the SNS female thread 1/4″ NPT pressure regulator suitable for 0-150 PSI applications.
- Thread: 1/4 NPT
Prices pulled from the Amazon Product Advertising API on:
Product prices and availability are accurate as of the date/time indicated and are subject to change. Any price and availability information displayed on [relevant Amazon Site(s), as applicable] at the time of purchase will apply to the purchase of this product.
About Air Compressors Regulators Video
As I noted in the video, regulators are devices that are used to change the pressure coming from the compressor receiver in all, or just part of, a downstream compressed air system, depending on where the air regulator is installed.
For example, you can have the main air pressure regulator (the one at the compressor tank) set for 120 PSI (30 PSI less than your tank pressure) and use the 120 PSI airflow to feed the air mains.
Then, at each application where compressed air is to be used, you can install another air regulator to further reduce the air pressure to the right level for just that air tool. Reducing air use, the energy cost to make the compressed air, and even extending the mean time between maintenance on the air tool due to the less rigorous forces at work.
FAQs (Frequently Asked Questions)
Yes, they are one of the most important components of an air compressor. Compressed air regulators are necessary in compressed air applications for a number of reasons, with the most important being that they give you the ability to set and control the downstream air pressure that will which your pneumatic tools.
Pressure regulators essentially control the air pressure and allow you to decrease it to match the needs of your desired application. As different levels of pressure are needed for different types of pneumatic tools, it’s important to have regulators so that you can alter the pressure to your specific tools’ requirements!
Without the function of a pressure regulator, a large volume of energy will be consumed daily to meet peak demands, even if your applications only require a little amount. So, the reason to regulate your air compressor is to properly serve your air tools, streamline applications, and save energy.
Reader Questions and Responses
How to Adjust the Regulator Gauge on Craftsman 3gal Air Compressor
Question:
I have a Craftsman 3 gal. Air Compressor, 1 hp, Horizontal Tank. Just got this compressor and I just wanted to know how you adjust the regulator gauge. I know I turn the knob but I just don’t know how to adjust it right, do I loosen it or tighten it, to regulate my air, the manual doesn’t tell you how to adjust.
Response:
I wrote the eBook The Home Compressor for folks just like you. The manufacturers write manuals, but they seem always to write them from the perspective of someone who already knows all the answers. This eBook is written for folks who don’t already know the answers and want to find out.
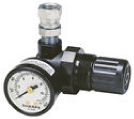
Typical air regulator – this one is installed with the adjusting knob on the side. The regulator will work in any orientation.
On the top of the regulator knob on my compressor, there’s an arrow that shows if you turn the knob to the right a plus (+) happens and if you turn the knob to the left a minus (-) happens. That means that turning the regulator knob to the right will increase the DOWNSTREAM pressure from the regulator.
I expect that your regulator will work the same way. Your compressor should have two pressure gauges on it. One shows the pressure inside the air tank, and the other, usually mounted on the regulator, shows the pressure setting that you have selected by turning the regulator dial.
If the gauge on the tank says 100 PSI and the gauge on the regulator says 80 PSI, as long as there is more than 80 PSI air pressure in the tank, the air tools or air-using devices downstream from the regulator will get a steady flow of air at 80 PSI.
If you have an air charge in your air tank (the compressor has run until the tank reaches the cut-out air pressure) then watch the gage on the regulator and turn the knob. As long as there is more pressure in the tank than you set on the regulator gauge dial, the needle will move as you turn the knob. Then you can see for sure which way to turn the knob on your regulator. Hope this answers your question.
Replacing a Regulator and Reconnecting It
Question:
I replaced the regulator and reconnected it to the compressor using “plumbers tape” I think that is what it is called but can not get the knob to move in either direction. The compressor fills with air but it continues to leak out the end opposite the gauge. which seems to have a plug in it. I have not connected the hose to it yet… maybe that would have helped?
Response:
If I am understanding you correctly, you used the plumber’s tape as a thread sealant. The use of plumber’s tape as a thread sealant isn’t a problem, as long as the tape end isn’t over any hole, causing a blockage or eventually allowing bits of tape to flow down the air line.
You go on to say “the compressor fills with air but it continues to leak out the end opposite the gauge.” I am not entirely sure what you mean by this.
Since I cannot see your regulator installation, I don’t know what is on the opposite end of the gauge. Just one quick check. Are you certain that the regulator is installed in the right direction? Regulators normally have an arrow on them showing the flow path of the air from the higher pressure side (tank side) to the application side (hose side). Make sure the regulator is oriented in the airline properly.
As far as adjusting the regulator goes, if you cannot turn the knob, try pushing it down or pulling it up. Some regulators have a mechanism where the handle disengages from the spindle inside. Pushing in, or pulling out, on the regulator handle re-engages the spindle. If that doesn’t help, please make another post, but this time, include photos so I can see what it is you are referring to.
If you have any questions regarding air compressor regulators please add a comment below along with photos if applicable so that someone can help you!