Hey! This site is reader-supported and we earn commissions if you purchase products from retailers after clicking on a link from our site.
An air compressor bogging down when running is a very common issue for users. This article will present to you the possible reasons why this is happening, reader questions and responses, and an opportunity for you to post about your problem and receive some help!
Table of Contents
- Why is an Air Compressor Bogging Down?
- Most Common Reasons for Air Compressor Bogging Down
- Most Frequent Cause of an Air Compressor Bogging Down & How to Test
- Youtube Demonstration
- FAQs (Frequently Asked Questions)
- Reader Questions and Responses
Why is an Air Compressor Bogging Down?
By that, I mean that the air compressor starts normally, it begins to build pressure in the tank, but at a certain point, the compressor motor begins to slow down.
The compressor motor begins to labor, the compressor motor slows, the sound changes, and the buildup of air pressure in the tank either stops completely or slows substantially.
Sometimes, when an air compressor bogs down, that process causes a problem with the power. The motor may pull too many amps, and the circuit breaker lets go. Or, the on-compressor thermal reset button will shut down the compressor due to motor overheating.
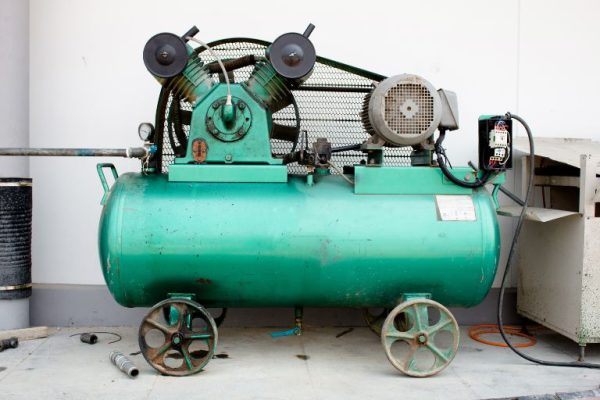
Most Common Reasons for Air Compressor Bogging Down
Diagnosis of the problem may not be that easy. There may be many things that can be the cause of the bogging down. Here are some of the most common reasons why an air compressor bogs down include:
- Use of a too-small extension cord to power the compressor. If an extension cord is being used, remove it, and plug the air compressor power cord directly into the wall socket to see if that helps.
- Use of a power bar to power the compressor. Same advice. Remove the power bar from the power supply and see if that helps.
- Too many other power-drawing appliances on the same circuit as the feed to the compressor. Ideally, an air compressor should be powered from a socket that leads directly back to a 15 amp (minimum) or a 20 amp breaker or fuse at the panel. If other appliances are in the line that feeds the compressor, shut them all down, and test the compressor again.
- The compressor unloader valve has failed. To test this, open the tank drain and let all of the air out of the tank. This will emulate the unloader valve function, and at the same time, remove water buildup in the tank. Close the drain and power up the compressor to test. If the compressor starts easily and runs up to cut out pressure, it’s time to service or replace the unloader valve.
The previous checks are simple. There is one more that you should do before getting to the more complex checks noted below.
If the compressor is belt-driven, remove the belt (power cord out please) and turn the pump sheave by hand. If it turns relatively easily with no binding, that helps eliminate the pump as the cause.
Most Frequent Cause of an Air Compressor Bogging Down & How to Test
The reality is that the most frequent cause of an air compressor bogging down on start-up is a failing start capacitor. It’s now time to test this component, visit our How To Test A Start Capacitor On Air Compressor Motor guide!
If the start capacitor checks out, and your compressor has a run capacitor, check that one next. If either is not up to snuff, they must be replaced.
Now it’s decision time. Do you take your compressor motor to an electric motor shop for a load check, or do you tear down the pump to see what’s what? Your rotating of the pump sheave may help.
If there was any hint that the pump may be malfunctioning mechanically, tear down the pump to check the piston rings, intake and pressure valves, and general condition of the pump innards.
If you feel that the compressor pump is okay, and the power supply to the motor and the motor caps are good, it may be time to pay for a motor load test.
If you opt for tearing down the compressor pump, depending on the age of the compressor and level of use (ie; did you forget to put oil in a lubed compressor?) you may want to replace the piston ring, valve plate, and ALL gaskets to ensure that when you reassemble the pump, none of these items can be an issue for some time.
Make sure when you install the valve plate that it is right side up, or else your compressor pump will not work.
One last thing, you should know the duty cycle of your air compressor and make sure you run the compressor within this time frame. Overuse of the compressor can be a factor in why an air compressor is bogging down.
Youtube Demonstration
I have picked out a useful YouTube demonstration that may help you with your bogged-down compressor!
FAQs (Frequently Asked Questions)
It is likely that any of the following reasons could be the cause of your air compressor bogging down: extension cord use, too many power-drawing tools, a failed unloader valve, or a failed capacitor.
Weakening of the insulation around individual wires in the motor coils tends to be the beginning of electrical failures in the motor that cause bogging down. Thermal stress, contamination, and movement of the winding due to magnetic forces in motor start-up and shut-down are the main causes of this weakening.
Reader Questions and Responses
The compressor bogs down at 20lb pressure and will not kick out?
Question
When I turn the compressor on it builds to 20lbs and then the motor bogs down and won’t kick out. There is a new pressure switch on it. The compressor sat for years without running so I drained the oil and refilled it. It still does the same thing. Any ideas?
Response
Scott,
Are you saying that it worked fine after the many years of sitting, or are you saying that the first time you used it since it sat, it bogs down at 20 PSI?
Make sure your compressor is getting clean power, no extension cords, and check the intake filter to make sure it is clean as well.
More info, please. What make of compressor, what model number, and what voltage?
The Compressor Kicks On but Sounds like the Motor Is Bogged Down
Question
2hp motor air compressor. Initially builds pressure to 115 psi. After it turns off it sits and does not look or lose pressure.
When the compressor does kick on, it sounds like the motor is bogged down and never builds pressure back. Stays around 20-30 psi and won’t build past this amount UNLESS I unplug the power cord and plug it back in.
I can’t find any leaks and upon checking the reed/flappers.
I now smell burnt oil, the top of the valve smokes from burning oil, and it’s very hot. So hot it melted the plastic threads on the filter housing!
So, I imagine I didn’t install the roads correctly. do I need a new reed/flap set? Why will the compressor build 1115 psi and then not unless power is disconnected?
I can’t afford a new, used one and really need this air compressor to finish siding my home for homeowners. Any help is most gratefully appreciated.
Response
Michael, you don’t indicate what make or size the compressor is, or what the power supply is. Tell me about the extension cord you are using. That may be an issue.
That your motor is overheating suggests that you’ve got…
a) a power supply problem
b) a motor problem
c) a start/run capacitor problem
d) an unloader valve that isn’t working properly
e) a valve/gasket problem
Air Compressor Bogs Down
Question
I have a 60gal 3hp air compressor. Worked great until last week.
I decided to fix it up after many years of faithful service.
The 5hp motor was having a hard time so I got a new 3hp (No 5hps are available and since it was a 3hp head WhatTheHell) it worked great one time but the pressure switch was going out.
I replaced the bent and dented old copper tubes with new ones.
I replaced the switch but now the motor bogs down upon reaching 50lbs and the motor STRAINS and pops the breaker. the head gets really hard to turn until it bleeds off thru the valve by the pressure switch then it’s ok until it gets hard to run and the motor bogs again. NOTHING was actually changed in regard to the head. Just the switch, motor, and tubes. Why is it bogging down? I’m afraid I’ll fry the new motor at this rate. Why is the head acting up?? what can I do about it?
Response
JC, this part of your post confuses me: “I have a 60gal 3hp air compressor” and “The 5hp motor was having a hard time so I got a new 3hp”
I surmise that you are powering it with 240 VAC as a 5HP sure wouldn’t run on 110 AC power.
If the original motor was a 5 HP, putting a 3HP on that pump would likely cause the problem. The motor bogs down because it cannot overcome the load being developed by the pump.
If the original motor was a 3 HP, and someone put a 5 HP on it, perhaps they changed the sheaves then, and the wrong size sheave could contribute to the problem.
Remove, clean and replace the tank check valve and see if that helps.
If you have any questions regarding an air compressor bogging down, please leave a comment below, with a photo if applicable, so that someone can help you!